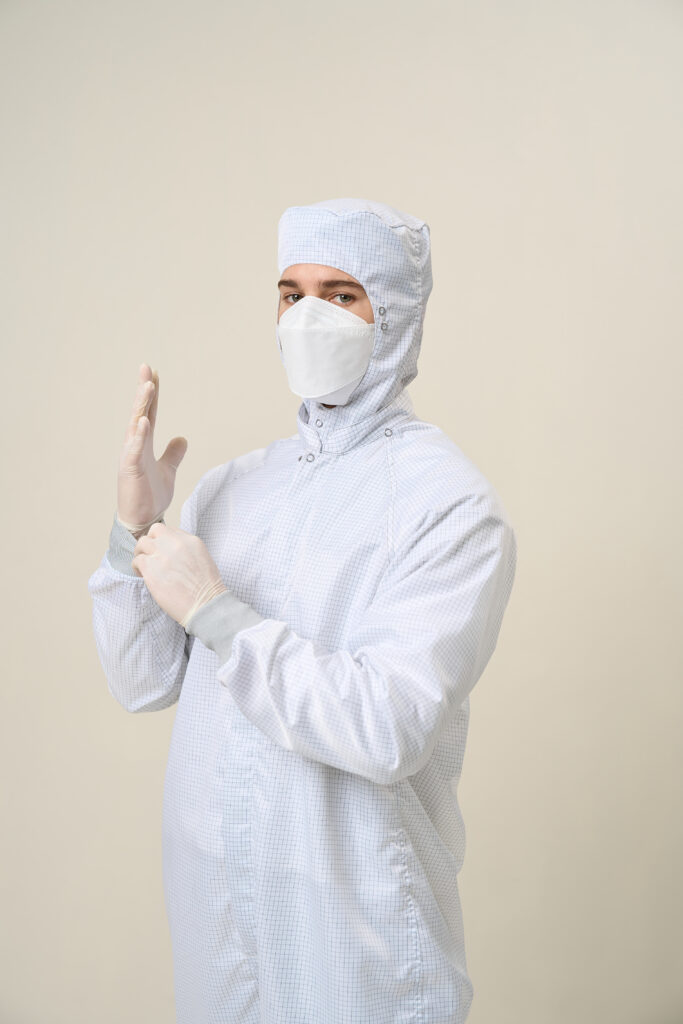
In cleanrooms, where constant interaction between personnel and products occurs, specific environmental factors—such as controlled airflow, low humidity, and the nature of cleanroom materials—contribute to a variety of electrostatic phenomena. These conditions can result in electrostatic discharge (ESD), which poses risks to products and equipment by attracting unwanted particles and causing subtle but significant issues. These include altering the cleanroom environment, generating unintended particle events, and disrupting equipment performance. Such challenges not only lower productivity but also complicate maintenance efforts. Therefore, controlling electrostatic charges in a cleanroom environment is crucial for ensuring efficient manufacturing processes. Grounding techniques and the use of static-dissipative materials are essential in mitigating the risks associated with ESD.
IEST-RP-CC052 is a practice designed to help cleanroom professionals prevent and eliminate electrostatic charges. It provides an understanding of electrostatic charge phenomena and the basis for charge control protocols. Appendix D, “Cleanroom Garment Considerations for an Electrostatic Discharge Program,” outlines requirements for garment fabrics, dissipative fabric specifications, and garment construction. Similarly, ANSI/ESD S20.20, the ESD Association Standard, defines the requirements for developing an electrostatic control program to protect electrical and electronic parts, assemblies, and equipment. According to ANSI/ESD S20.20, “all conductors in the environment, including personnel, shall be bonded or electrically connected and attached to a known ground or contrived ground.”
In compliance with both IEST-RP-CC052 and ANSI/ESD S20.20, we have developed an ESD Cleanroom Garment that incorporates the following critical grounding and continuity points:
– hood to coverall
– sleeve to body
– cuff (BCP)* to sleeve
– coverall to boot
– boot sole (BCP)* to floor
*Body Contact Point
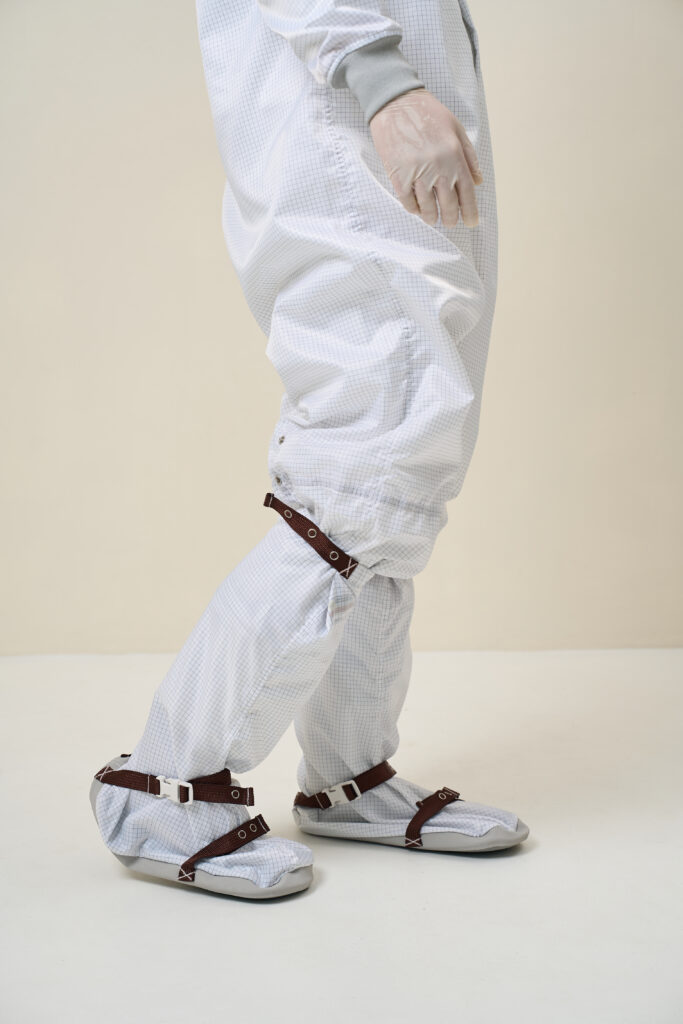
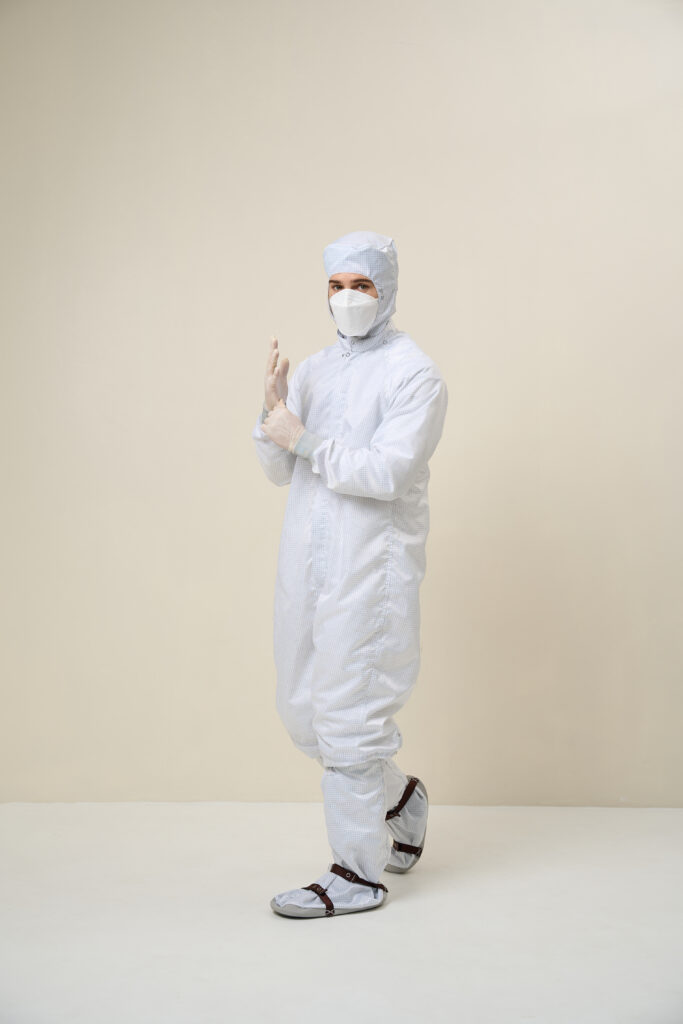
This ESD Cleanroom Garment System is fully groundable, from head to boot, and is created using ISO 6 static dissipative fabric. Each component—hood, coverall, and boots—is connected with conductive thread, tape, and ground snaps. Conductive boot soles remove static charges from personnel through the cleanroom’s ESD floor or mat. Therefore, this design maintains electrical conductivity throughout the garment seams, creating a continuous electrical path from the hood and wrist cuffs to the boots and ensuring compliance with IEST-RP-CC052.1 and ANSI/ESD S20.20 standards. Furthermore, the system provides consistent continuity readings for up to 100 wash cycles.